« LA PRODUCTION DE PETITES SÉRIES EST DANS MON ADN »
09 septembre 2021
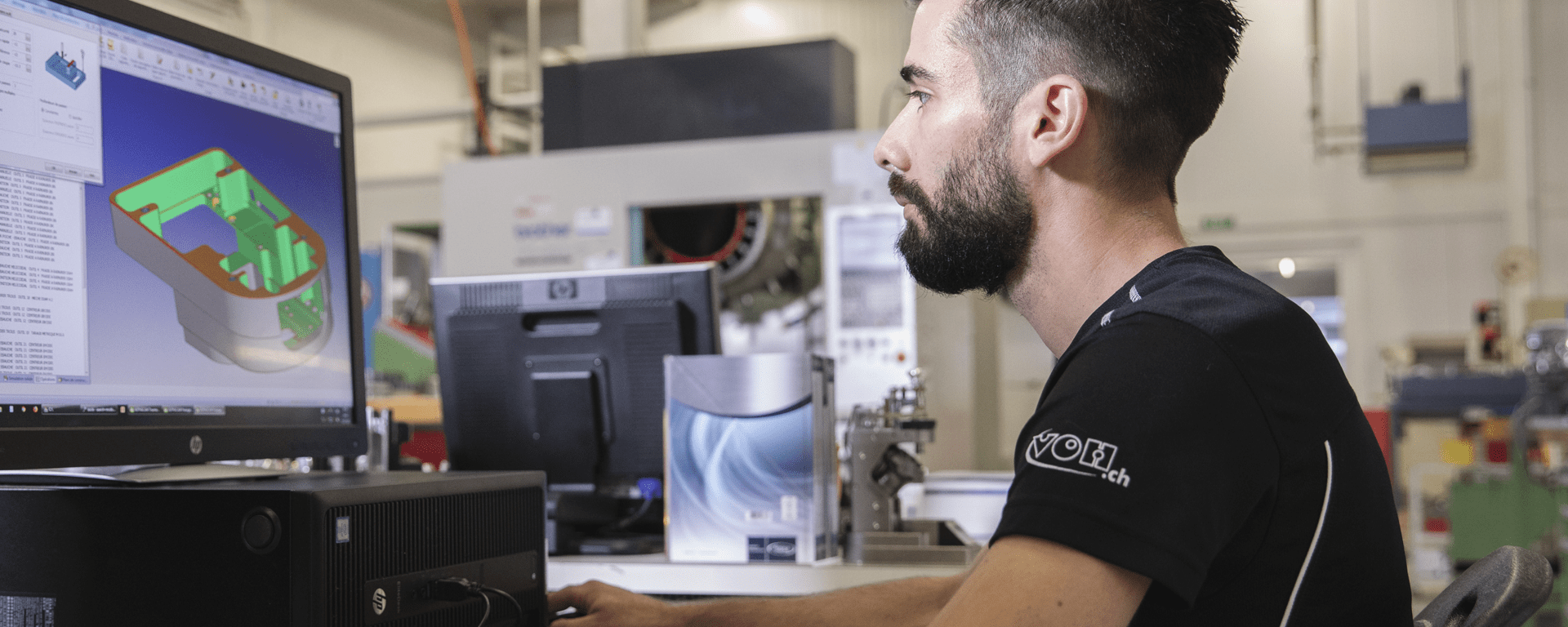
Bastien Zbinden est responsable de l’usinage chez VOH SA. Au bénéfice d’un CFC de polymécanicien et technicien ES en productique/exploitation, le jeune homme est actif au sein de notre entreprise depuis cinq ans déjà. Le concept d’usinage est placé sous sa responsabilité avec comme leitmotiv : viser un maximum de flexibilité dans une production qui comporte essentiellement des petites séries de pièces pour une grande variété de produits.
Il occupe un poste multitâche : outre l’optimisation des processus de fabrication, il participe notamment aux études destinées à obtenir les pièces les plus compétitives possible. Ajoutez-y la gestion complète du département : ressources humaines ou maintenance du matériel, et nous obtenons une vision qui reste encore partielle du large panel des tâches du polymécanicien de formation.
« Notre concept d’usinage est complexe. On usine de petites séries, cela implique d’être très flexible dans notre programmation et notre mise en train », explique d’emblée Bastien Zbinden. En effet, au sein du département usinage, la fabrication d’une pièce se décline en trois étapes : le temps de programmation, le temps de mise en train, et enfin le cycle d’usinage. La durée des phases est variable selon les complexités, mais très grossièrement, chacune d’entre elles s’évalue entre deux et quatre heures.
VOH fabrique la presque totalité de ses produits en interne et assure même son approvisionnement en quasi totale autonomie. « Nous avons une grande variété de produits qui eux-mêmes contiennent de nombreux composants à usiner », précise le polymécanicien. Et les pièces à produire ne sont que des petites séries, mais très variées. On passe facilement d’une pièce de quelques millimètres le matin à une pièce de 500 mm l’après-midi. On le constate, l’optimisation de cette partie-là de la production de VOH nécessite une véritable organisation. « Dans notre philosophie, nous devons nous focaliser sur notre temps de programmation et sur la mise en train, pas sur le cycle d’usinage. »
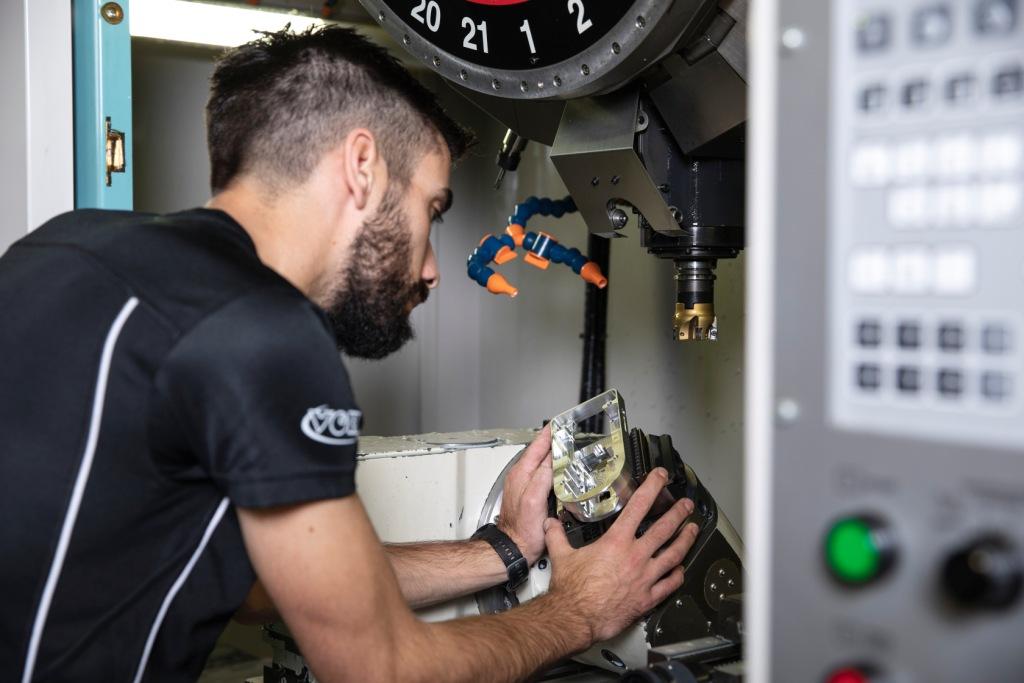
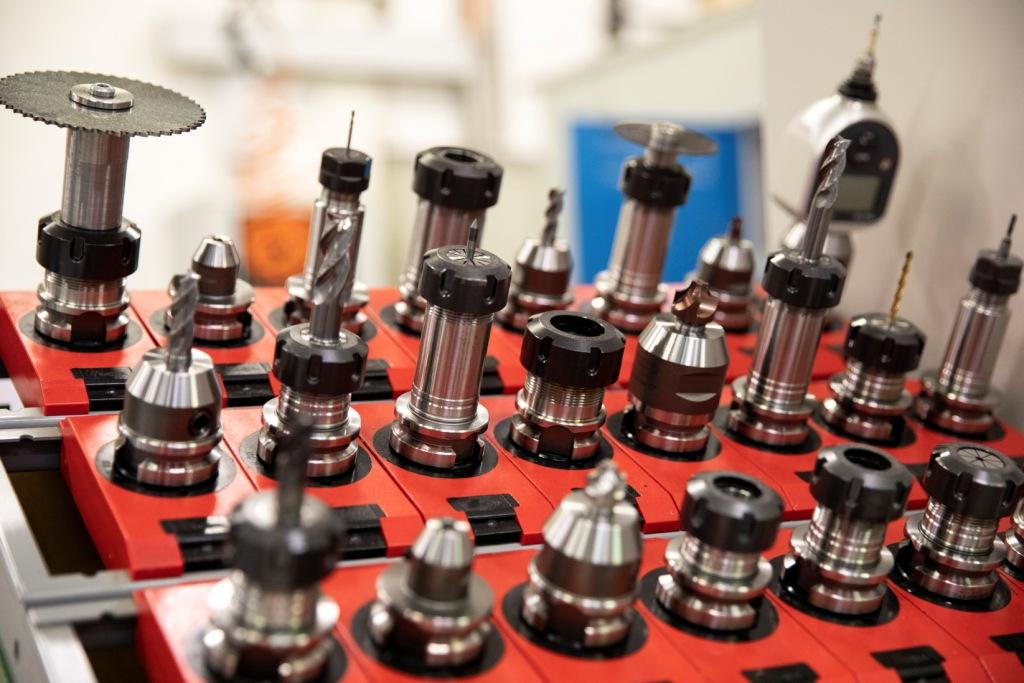
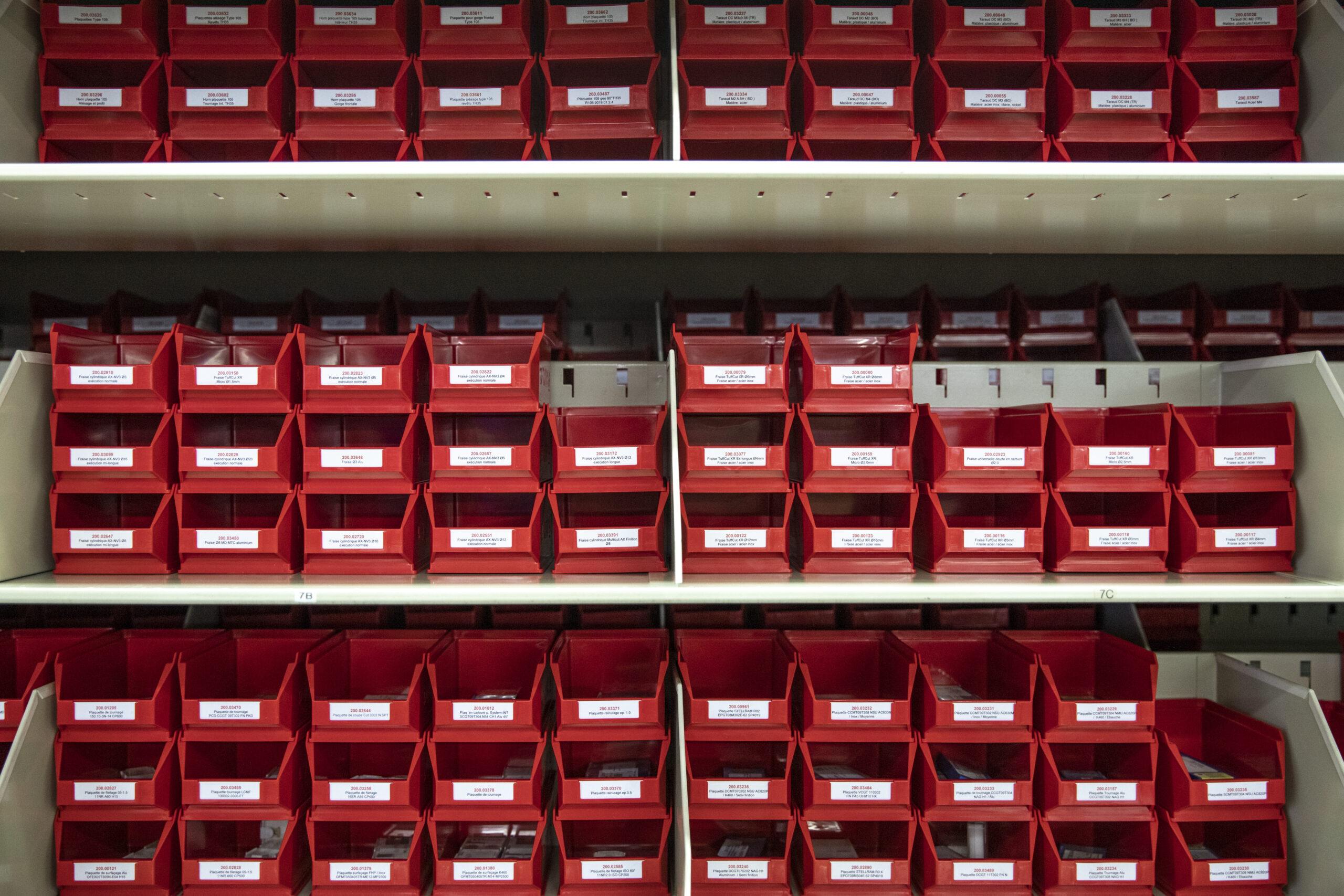
UNE ORGANISATION AU MILLIMÈTRE
Ainsi, dans l’atelier, tout le flux de travail est organisé autour des postes informatiques qui sont placés, en croix, au centre de la zone de production. « Ce qui permet d’optimiser les déplacements de chacun. » Autour, on retrouve les différentes unités de production (CNC, tour automatique, etc.). Afin d’atteindre les objectifs fixés, plusieurs procédures ont été mises en place : cela débute justement par l’organisation des documents informatiques. « En collaboration avec l’entreprise MW Programmation, nous avons mis en place un système d’organisation de nos fichiers, intégré au logiciel Alphacam, qui nous permet de retrouver très rapidement les programmes dont nous avons besoin. » L’infrastructure implantée permet de documenter très précisément une opération d’usinage en y liant tout type de document, fichier ou texte. Un champ « Remarque » permet également à l’opérateur de visualiser l’historique des événements marquants de la dernière série produite. « Cette organisation facilite la suite du travail du mécanicien. »
Démonstration à l’appui, Bastien Zbinden imprime une feuille de fabrication. Le document, format A4, comporte toutes les informations nécessaires à une mise en train, une sorte de check-list avec le type de programme à transmettre à la machine, le type de matière à charger ou encore les outils de coupe nécessaires à la production. Ainsi, il suffit de suivre les indications de la feuille. Et de nombreuses petites astuces assurent un gain de temps. Par exemple, dans l’armoire à outillage, le numéro des outils est directement gravé, ce qui permet de les repérer plus vite lorsqu’il s’agit de récupérer ceux dont on a besoin. « Dans l’approvisionnement, on ne recherche pas les outils de coupe les plus performants du marché. On sélectionne ceux qui permettent de travailler dans n’importe quelle condition. »
« NOUS SOMMES TOUS DES PROTOTYPISTES »
Du côté des six collaborateurs et de l’apprenti travaillant dans ce secteur de l’usine, tout est flexible. « Chacun d’entre nous peut travailler sur n’importe quelle machine alors qu’habituellement, c’est plus restreint. » Ainsi, un mécanicien suit la production d’une pièce du début jusqu’à la livraison finale. « On est surtout des prototypistes, pas des spécialistes d’une seule discipline, tel le tournage ou le fraisage », explique Bastien Zbinden. Et chez VOH, on peut le dire, les apprentis apprennent la flexibilité. Le responsable de l’usinage rappelle que ceux-ci ont la possibilité de concevoir 100% du programme. « Ils ont la liberté de réaliser une pièce selon leur vision. » Ainsi, ils progressent au fur et à mesure de la découverte des différents centres de production.
Côté organisation, la gestion de petites séries demande beaucoup d’efforts. Bastien Zbinden en plaisante : « Leur conception et leur optimisation sont dans mon ADN ! » L’organisation passe donc par un planning hebdomadaire qui doit être le plus cohérent possible : « Entre chaque matière, il faut nettoyer la machine, ce qui prend vite trente minutes. Il faut donc être rationnel dans l’organisation des différentes séries à produire en travaillant en fonction des matières à usiner, par exemple. »
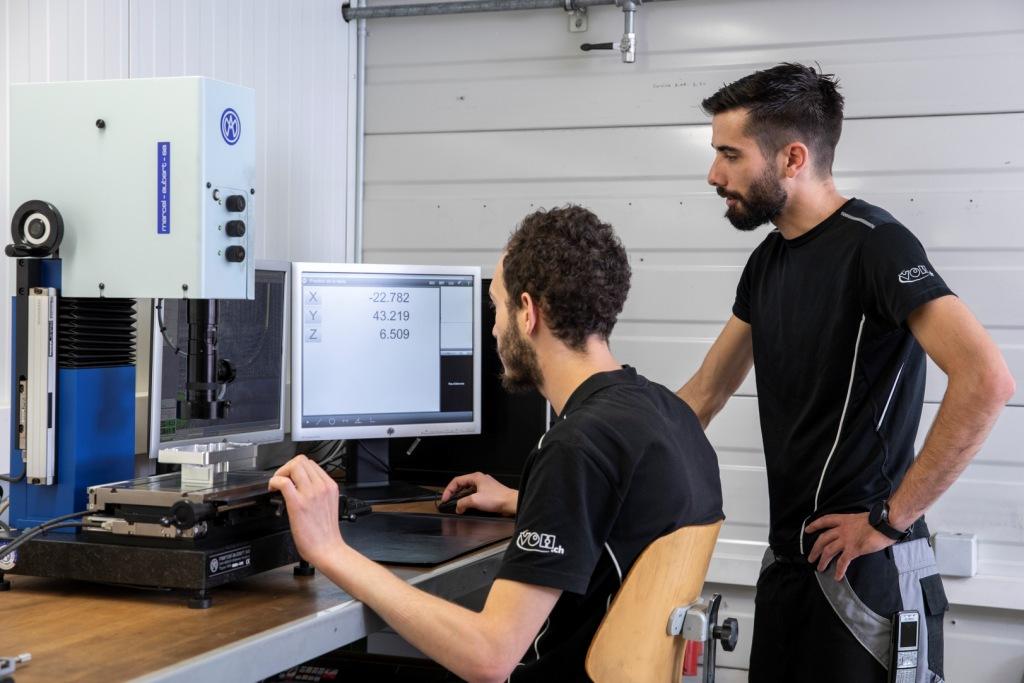
DES GANTS DE VELOURS
Lors du contrôle final de série, chacun est face à ses responsabilités. C’est le mécanicien chargé de la production qui vérifie la qualité de son travail. « Ce changement de stratégie par rapport au passé est un succès : on n’a quasiment plus aucune série de pièces qui nous revient en retour. » Ainsi, le mécanicien a véritablement un rôle clé au sein du concept d’usinage de VOH.
Et Bastien Zbinden résume bien la philosophie de l’entreprise : « Nous produisons pour des horlogers. Nous devons donc soigner nos pièces. La rigueur et la vigilance sont de mise, particulièrement lors de leur manipulation, presque comme si nous portions des gants de velours. »