“SMALL PRODUCTION RUNS ARE PART OF MY DNA”
September 9, 2021
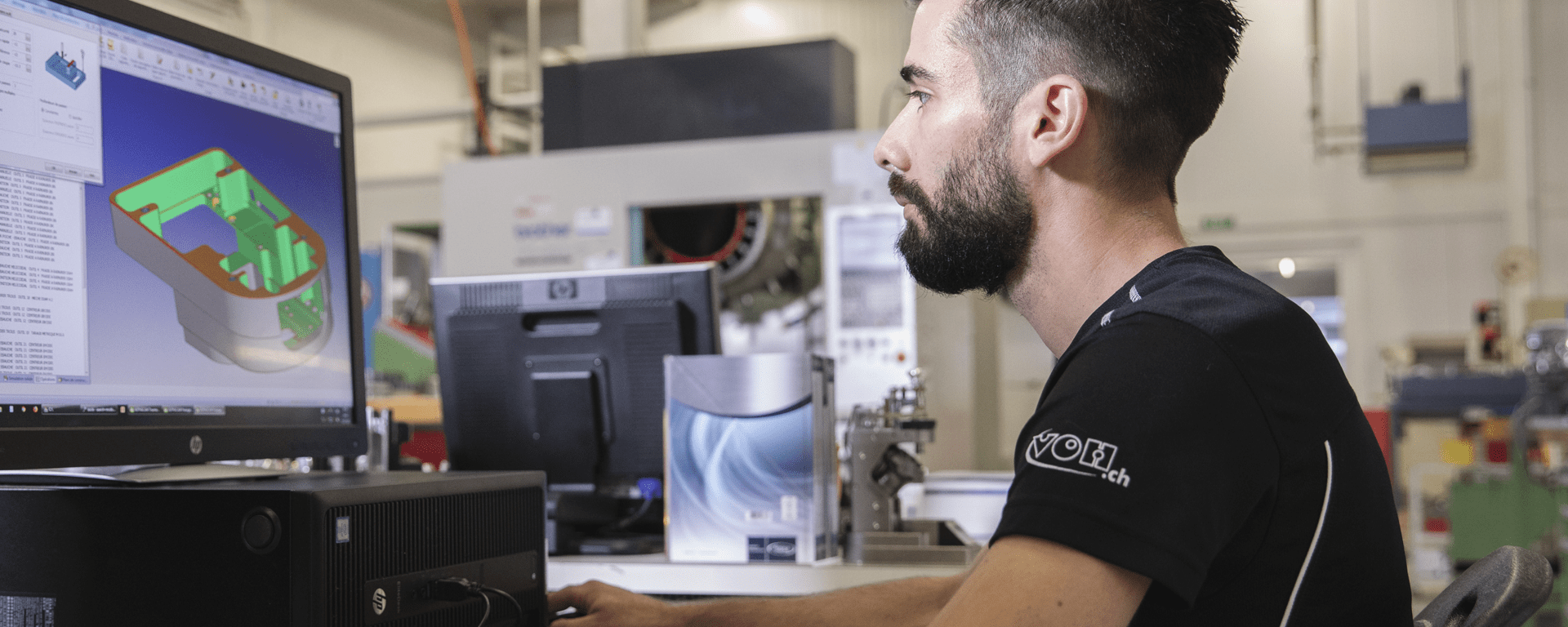
Bastien Zbinden manages machining at VOH SA. With the advantage of a poly-mechanics CFC [Federal certificate of capability] and as a Graduate manufacturing technology/operations technician, this young man has been working our company for five years. The concept of machining is placed under his responsibility as a Leitmotif: the pursuit of a maximum degree of flexibility in production that mainly involves small production runs of parts for a wide variety of products.
Bastien Zbinden has a multi-tasking role: in addition to the optimisation of manufacturing processes, he is mainly involved in studies for making parts as competitively as possible. Add to this the overall management of the department: human resources or equipment maintenance, and we have some kind of (still partial) vision of the wide range of tasks of this trained poly-mechanics specialist.
“Our machining concept is a complex one. We machine in small production runs, and this entails being very flexible in our scheduling and set-up time”, Bastien Zbinden explains. In fact, within the machining department, the manufacturing of a part is divided into three stages: programming time, set-up time, and finally, the machining cycle. The duration of the phases is variable according to the complexities involved, but very broadly, each of these are assessed for between 2 and 4 hours
VOH manufactures almost its products internally, and even provides its own supplies almost completely autonomously. “We have a wide variety of products which themselves contain numerous components to be machined”, as the poly-mechanics specialist explains. And the parts to be produced are only small production runs, but very varied. One can easily move from one part only a few millimetres in size in the morning to a part 500 mm in size in the afternoon. We have determined that the optimisation of this part of VOH’s production requires a thorough-going organisational structure. “In our philosophy, we need to focus on our programming and set-up, rather than on the machining cycle.”
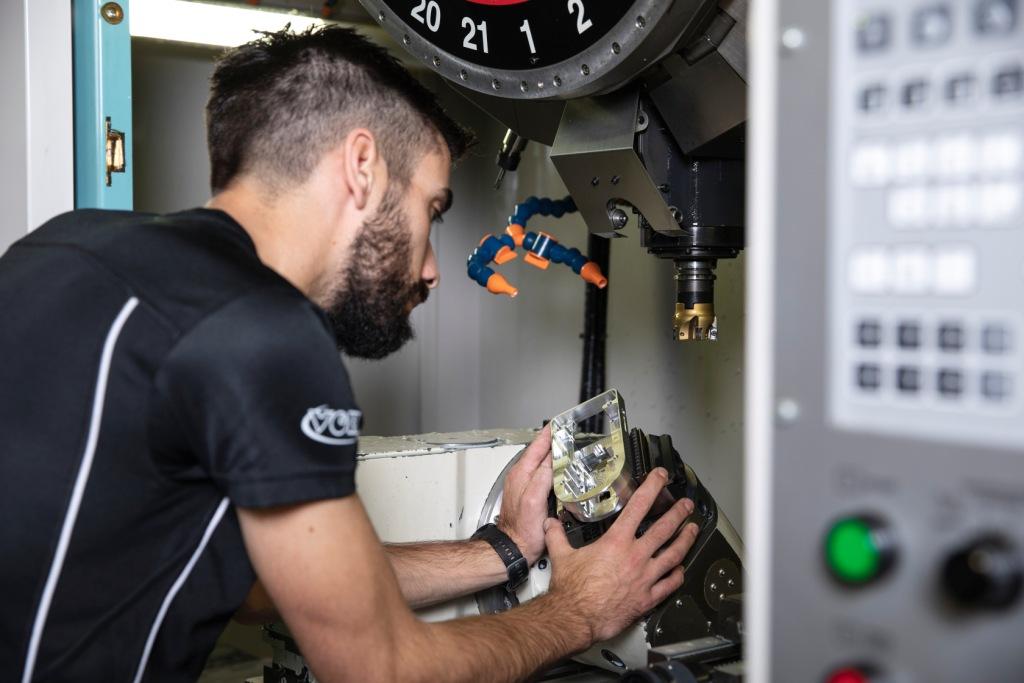
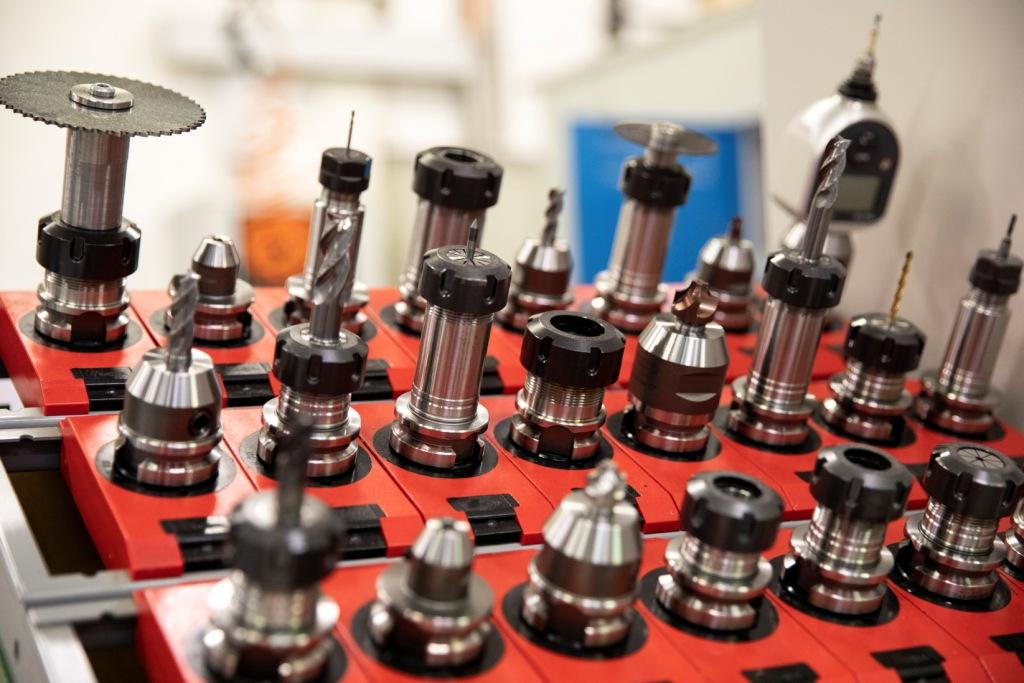
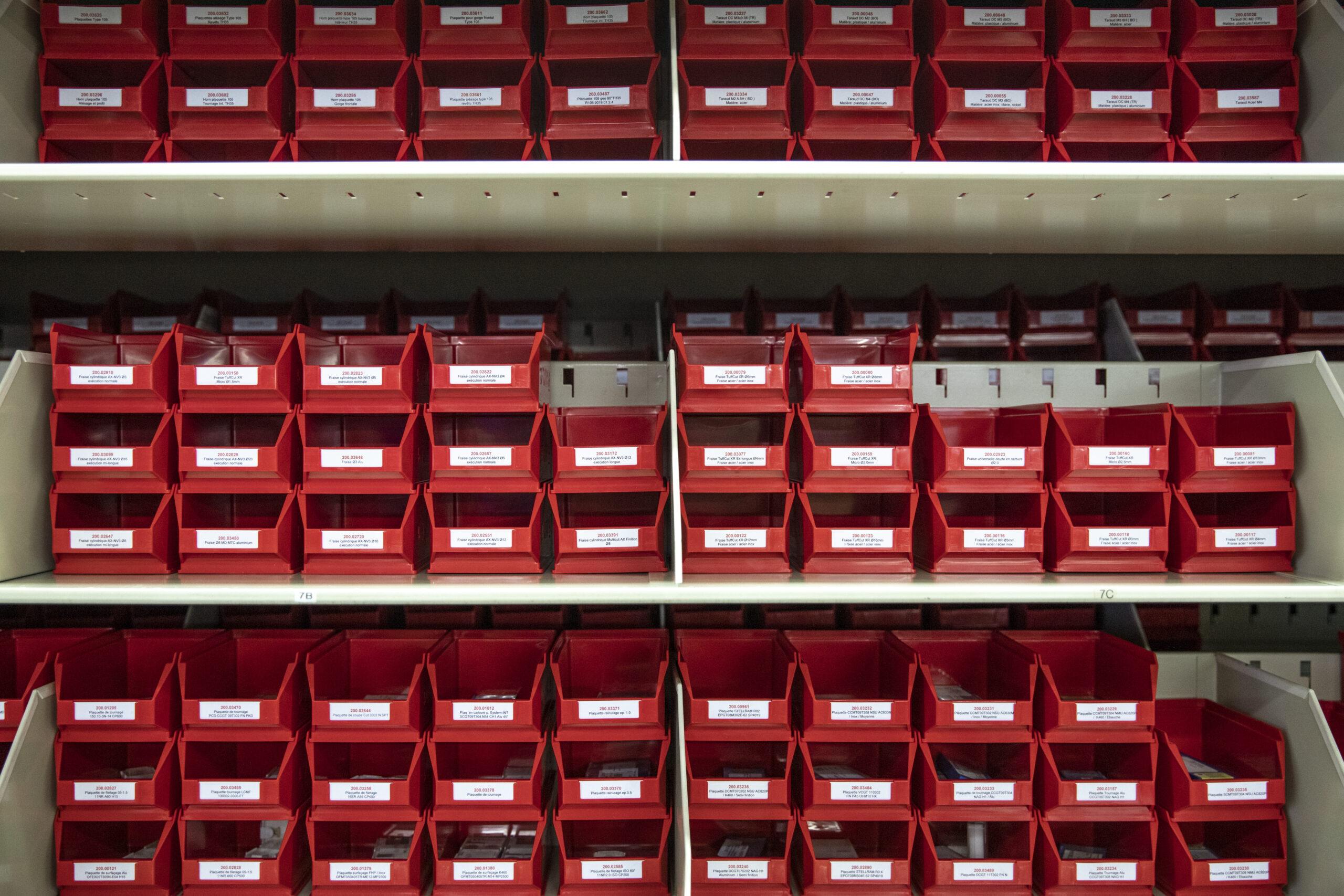
ORGANISATION TO THE LAST MILIMETRE
Thus, in the workshop the entire workflow is organised around computerised workstations which are located in cross form, at the centre of the production zone. “This enables the optimisation of everyone’s movements.” Around this we find the various production units (CNC machines, automatic lathe, etc.). In order to achieve specified objectives, many procedures have been put in place: this starts with the organisation of computer documents. “In collaboration with the company MW Programmation, we have established an organisation system for our files incorporated in Alphacam software, which enables us find the programs we need very quickly.” The infrastructure that has been set up enables very precise documentation of a machining operation linking to it all types of document, file, or text. A “Comments” field also enables the operator to view the background of key events of the previous production run. “This organisation facilitates the mechanic’s subsequent work”.
By way of supporting demonstration, Bastien Zbinden prints a manufacturing data sheet. The document, in A4 format, contains all the information necessary for setting up, a sort of checklist with the type of program to be sent to the machine, the type of material to load, or the cutting tools required for the production. This means that all that is required is to follow the data sheet instructions. And a large number of little tips mean time saved. For example, in the tooling rack, the tool number is directly engraved, which means that tools can be found more quickly when needed. “In supply, we are not looking for the most effective cutting tools on the market. We select those that enable us to work under any conditions.”
“WE ARE ALL PROTOTYPERS”
With the six colleagues and apprentice working in this division of the factory, everything is flexible. “Each of us can work on any machine, whereas this is something that is usually more restricted.” A mechanic therefore follows the production of a part from the start, through to final delivery. “We are prototypers above all, not specialists in a single discipline, such as turning, or milling”, explains Bastien Zbinden. And at VOH, it can be said that apprentices learn flexibility. The machining manager explains that they have the possibility of designing 100% of the program. “They are free to create a part as they envisage it.” They therefore progress incrementally with the discovery of the production centres.
This organisation, and the management of small batch production runs requires a great deal of effort. Bastien Zbinden comments light-heartedly: “Their design and optimisation are part of my DNA!” The organisation involves a weekly schedule which need to be as cohesive as possible: “Between each material, the machine needs to be cleaned, which can easily take thirty minutes. One therefore needs to be rational in the organisation of different batches to be produced according to the materials to be machined, for example.”
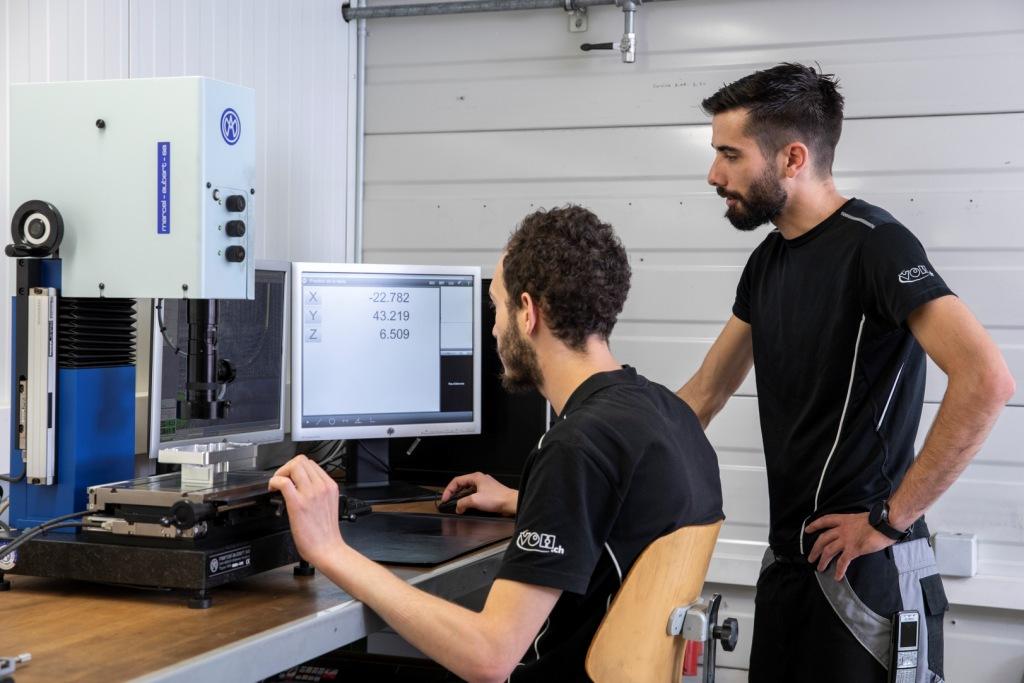
VELVET GLOVES
At the final check on the production run, everyone is accountable and responsible. The mechanic in charge of the production checks the quality of their work. “This change of strategy from previous practices has been a success: we almost never have a production batch returned to us.” The mechanic therefore really has a key role at the heart of the VOH machining concept.
And Bastien Zbinden summarises the company’s philosophy well: “We are manufacturing for watchmakers. We must therefore take very great care with our parts. Rigour and vigilance are mandatory, particularly in their handling, almost as though we were wearing velvet gloves.”